Some of the courses have mandatory workshops. The workshop is included in the course. Taking the course would be equivalent to physically taken the course at LSTC since they are taught by the same instructor. Each workshop is described by the instructor and time will be given to perform each workshop by the instructor or independently by the students. The students can talk to the instructor online or using phone or VOIP (the workshop course is very interactive with the instructor) at any time they desire. At the end of the workshop course the instructor provides all the solutions to the workshops in a pdf file. Some of the courses the workshop will be conducted by the instructor in a life manner.
Course Notes Can be Purchased Separately if Desired
Sample Course Notes
Workshop Descriptions
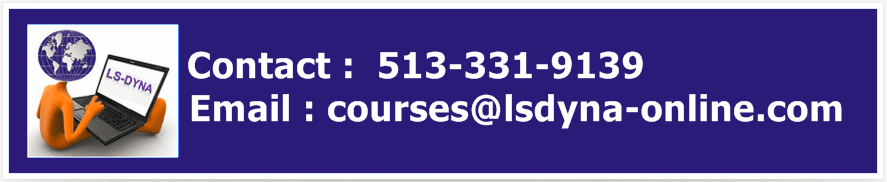
WORKSHOP DESCRIPTION
LS-DYNA FSI
Introduction
1. When to use Eulerian and ALE
2. Sample applications
Eulerian capabilities
1. Euler and ALE element library
2. Boundary conditions
3. Equations of state
Basic concepts of arbitrary Langrange-Euler (ALE)
1. When to use ALE
2. Advantages of ALE formulation
Basic concepts of Multi-Material
1. When to use multi-material
2. Advantages of multi-material formulation
Basic concepts of fluid/structure coupling
1. Different coupling methodologies
2. When to use them
Modeling techniques
1. Mesh design
2. Problem initialization
3. Post-processing
COURSE DESCRIPTIONS
Intro LS-DYNA
This course will allow first time LS-DYNA users to get started with minimal effort. The most important elements to start using LS-DYNA successfully will be presented in the 16 hours with about 8 hours of workshop.
- Chapter-0 : Introduction – LS-DYNA Manager
- Chapter-1 : Introduction to LS-PrePost
- Chapter-2 : Minimum Requirement to Run LS-DYNA
- Chapter-3 : Choosing Elements
- Chapter-4 : Choosing a Material Model
- Chapter-5 : Applying Loads
- Chapter-6 : Initial Conditions
- Chapter-7 : Boundary Conditions
- Chapter-8 : Defining Contact
- Chapter-9 : Output Control and Databases
- Chapter-10 : Critical Time Step
- Chapter-11 : Hourglassing
- Chapter-12 : Connecting Parts
- Chapter-13 : Damping
- Chapter-14 : How To Tell If Your FE Model Is Correct
- Chapter-15 : Summary
- Chapter-16 : Other Courses & References
LS-DYNA Implicit
Fracture, Damage, and Failure in LS-DYNA
Course Outline
Introduction and Historical Review
- Brittle Failure
- Ductile Failure
Introduction and Fundamental Theoretical Concepts
- Failure Theories
- Damage Models
- Fracture Mechanics
Element Erosion Advantages & Short Comings
Current LSDYNA Capabilities to Model Failure and Damage
Current LSDYNA Capabilities to Model Fracture
Fracture in Lagrangian, Eulerian, SPH, XFEM, EFG, and DEM Methods
LSDYNA Fracture Capabilities Verification examples
MAT_ADD_EROSION and the GISSMO Model
Material Models with Failure
- Isotropic Materials
- Hyperelastic Materials
- Composite Materials
- Geotech Materials
Modeling Delamination and Debonding in LSDYNA
- Cohesive Elements
- Tied Contact with Failure
Summary and Concluding Remark
